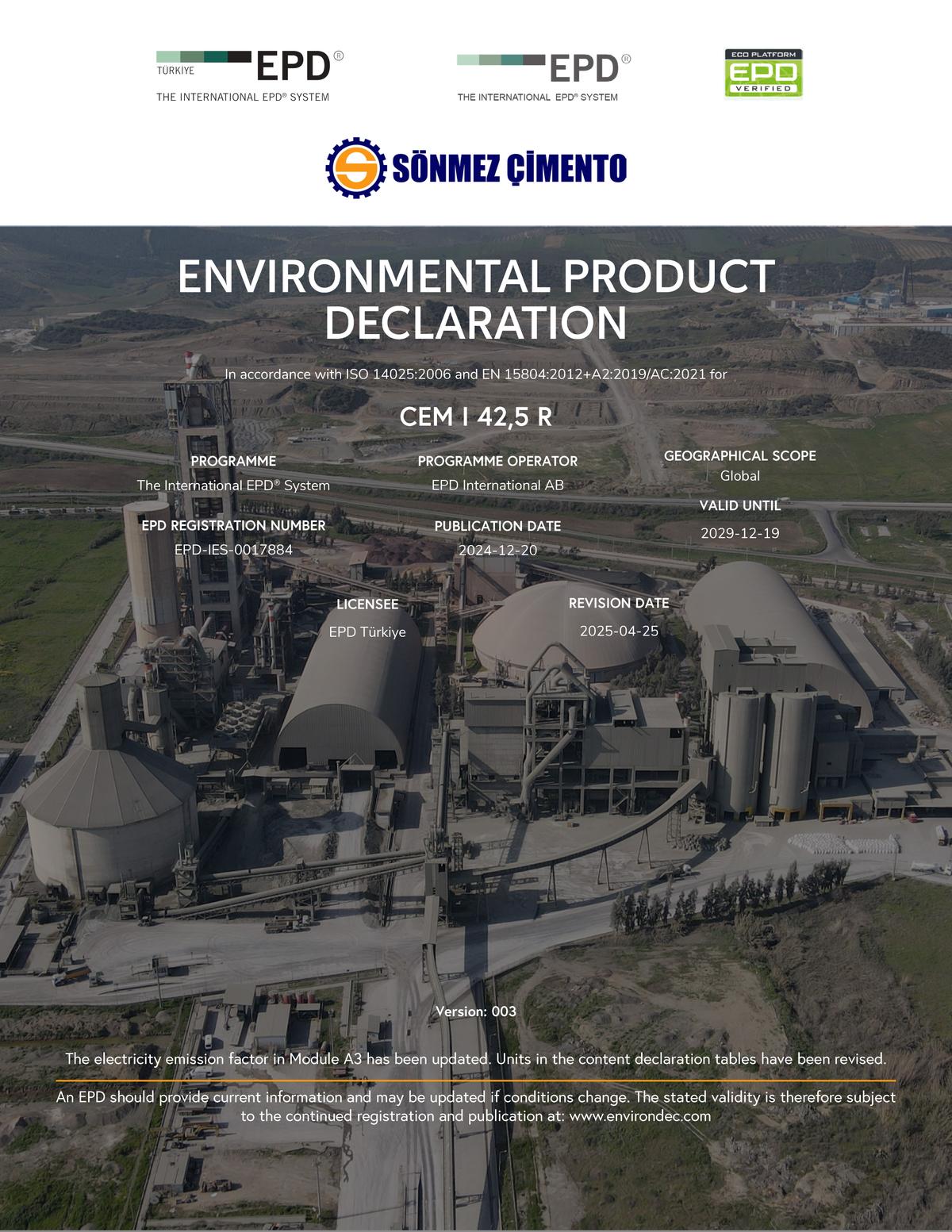
S-P-0017884
Sönmez Çimento Yapı ve Madencilik San. Tic. A.Ş.CEM I 42,5 R
The cement production process
begins with the extraction of primary raw materials, primarily limestone and
clay. These materials, along with marl and other naturally occurring resources,
are extracted from quarries and transported to the production facility. In
addition to these primary raw materials, other materials such as iron ore,
bauxite, and pumice may also be added to achieve the desired chemical
composition for the final product. Portland cement clinker is manufactured from
limestone, marl, clay, and iron ore/bauxite as corrector.
The raw materials are initially
crushed using crushers to reduce them to smaller sizes. Once crushed, the raw
mix is ground in a raw mill and called farin.
Farin is subsequently burned in a
rotary kiln at a temperature around 1.450°C. Partial fusion occurs, and nodules
of clinker are produced. During the burning process, the raw materials will
undergo complex chemical reactions and will eventually leave the kiln as cement
clinker. The clinker typically has a composition in the region of 67% CaO, 22%
SiO2, 5% Al2O3, 3% Fe2O3, and 3% other components, and normally contains four
major phases, called alite, belite, aluminate, and ferrite. Several other
phases, such as alkali sulfates and calcium oxide, are normally present in
minor amounts. The clinker produced in the kiln is cooled and stored in clinker
silos.
For the final production of cement,
the clinker is ground in the cement mill, where various additives are mixed in
to modify the properties of the cement. These additives may include substances
such as gypsum or fly ash, which are incorporated in varying proportions
depending on the specific type of cement being produced. The final product -
cement - is obtained by grinding the clinker to a fine powder, in a cement mill
together with minor/major additives and 3-4% of gypsum. The gypsum is a
necessary additive in order to retard the setting time of cement. This stage
allows for the adjustment of the cement's characteristics, such as setting
time, strength, and durability, according to the requirements of different
applications.
Finally, the finished cement is
stored in storage silos before being either packaged for shipment or
transported directly to construction sites or distribution points for use in
various construction projects.
CEM I 42,5R is commonly used in
various types of reinforced concrete buildings. These types of cement are
suitable for high-strength concrete applications, as well as for reinforced
concrete structures with thin sections. They are also ideal for buildings with
specialized requirements, high-rise reinforced concrete buildings, and
strengthening works for existing structures. These cements are extensively used
in the construction of bridges, viaducts, silos, and water tanks. Additionally,
they are used in road pavements, runways, and buildings constructed using slip
formwork or tunnel formwork systems. Another significant application is in
early-strength reinforced concrete production.
In industrial production, these
cements are used in the production of gas concrete, tile and ceramic adhesives,
and prefabricated, prestressed concrete elements. They are also utilized in the
manufacturing of railroad prestressed concrete ties, prefabricated reinforced
concrete building components, and for the production of concrete poles for
lighting and energy transmission lines. Other industrial applications include
the production of concrete pipes and curbstones.
CPC: 37440
14025:2006 and EN 15804:2012+A2:2019/AC:2021
Gallery
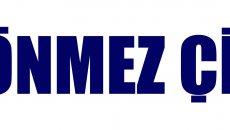
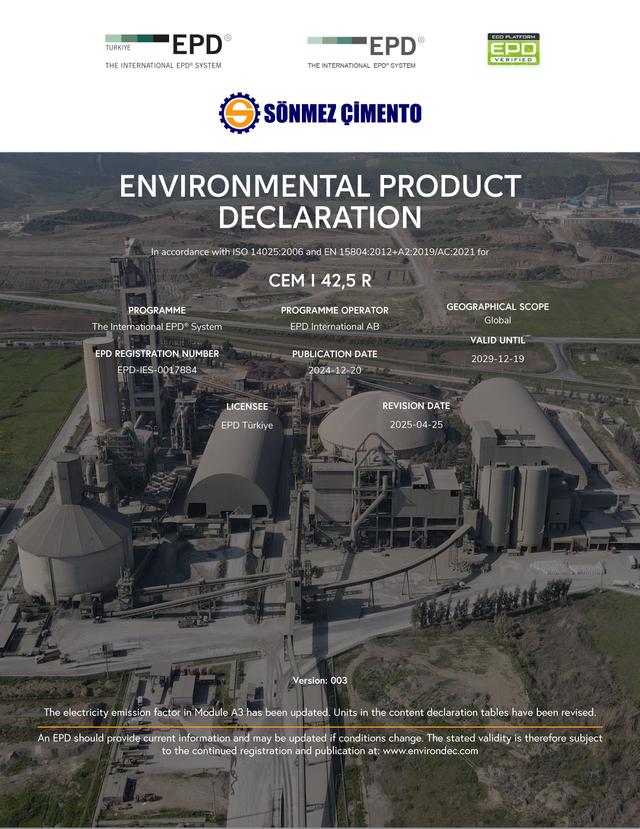
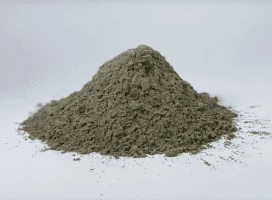
Registration & Validity
COMPANY INFORMATION
Sönmez Çimento Yapı ve Madencilik San. Tic. A.Ş.
Sönmez Cement, which was founded in December 2012 in partnership with Sönmez Holding, Kutlucan Holding and Türkün Holding, started production in Adana Yumurtalık Free Zone in September 2014 and made it’s first export in October 2014. Sönmez Cement, which employs more than 400 people with it’s 470-acre port and operating area in Iskenderun Bay, is the first and only cement factory established in free zones in Türkiye and also the largest chimney industrial facility.
With a production capacity of 2 million tons/year of clinker and 2.16 million tons/year of cement, Sönmez Cement exports more than 90% of it’s production. Designed in accordance with current environmental legislation with new generation dedusting systems, Sönmez Cement continues to be environmentally friendly with the use of alternative raw materials and by-products.
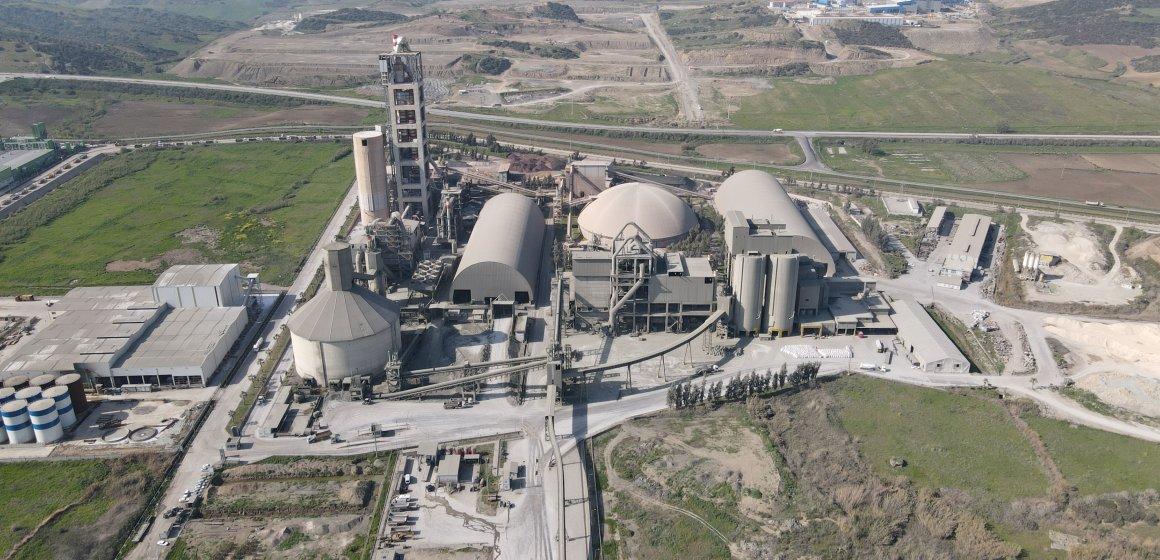
Contact
Adana Yumurtalık Serbest Bölgesi Sarımazı SB Mh. 2. Bulvar 5. Cadde No:5/01 Ceyhan / Adana / TÜRKİYE
0322 634 21 70https://www.sonmezcimento.com.tr/
See NowSönmez Cement, which completed it’s port operation in November 2017 and started loading clinkers and cement from it’s own port, opened the port business to third parties in February 2021 in order to support the country’s exports.
Sönmez Cement, which was
founded in December 2012 in partnership with Sönmez Holding, Kutlucan Holding
and Türkün Holding, started production in Adana Yumurtalık Free Zone in
September 2014 and made it’s first export in October 2014.
Sönmez Cement, which
employs more than 400 people with it’s 470-acre port and operating area in
Iskenderun Bay, is the first and only cement factory established in free zones
in Türkiye and also the largest chimney industrial facility.
With a production capacity of 2
million tons/year of clinker and 2.16 million tons/year of cement, Sönmez
Cement exports more than 90% of it’s production.
Designed in accordance with
current environmental legislation with new generation dedusting systems, Sönmez
Cement continues to be environmentally friendly with the use of
alternative raw materials and by-products.
Sönmez Cement, which
completed it’s port operation in November 2017 and started loading clinkers and
cement from it’s own port, opened the port business to third parties in
February 2021 in order to support the country’s exports.